Echuca Moama Bridge Project
MBB’s contributes directly to the success, safety & timely delivery of the long-awaited Echuca-Moama Bridge in Northern Victoria
.jpg)
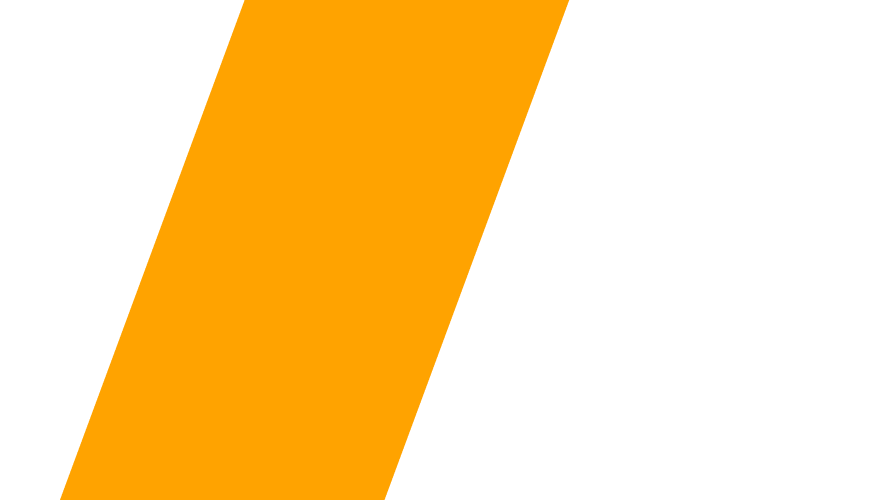
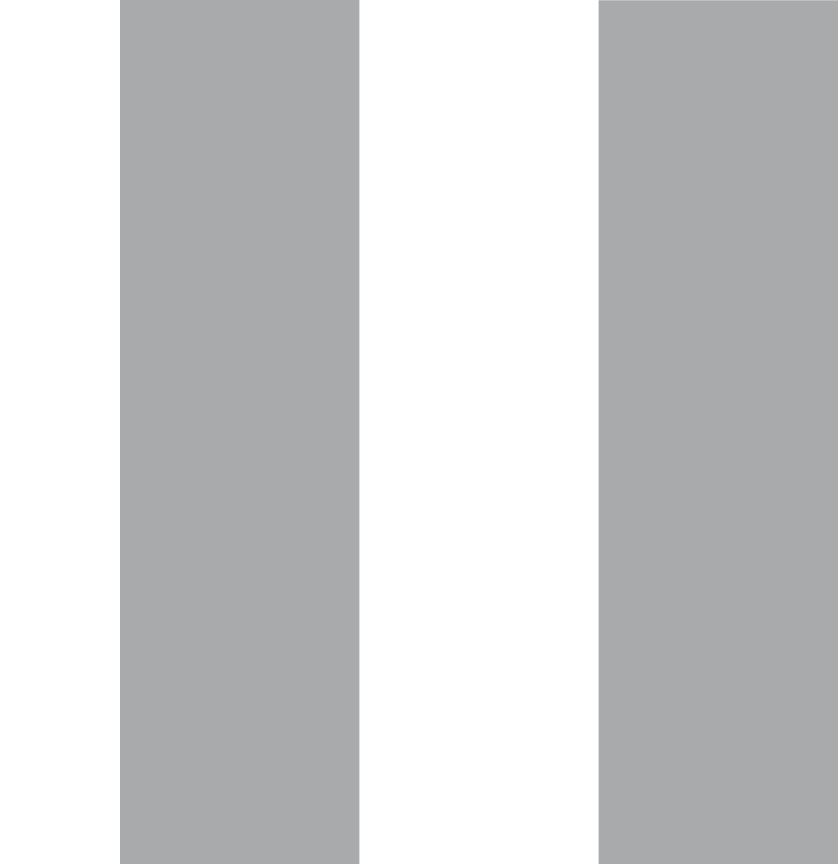
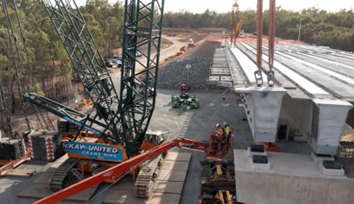
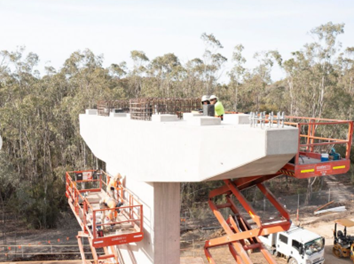
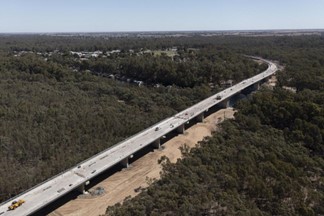
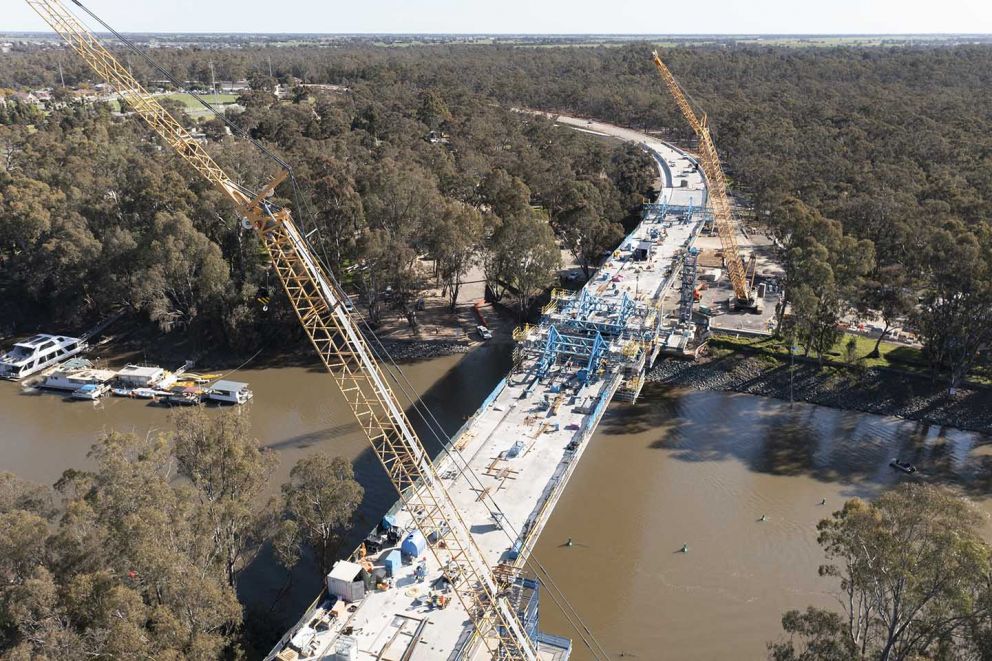
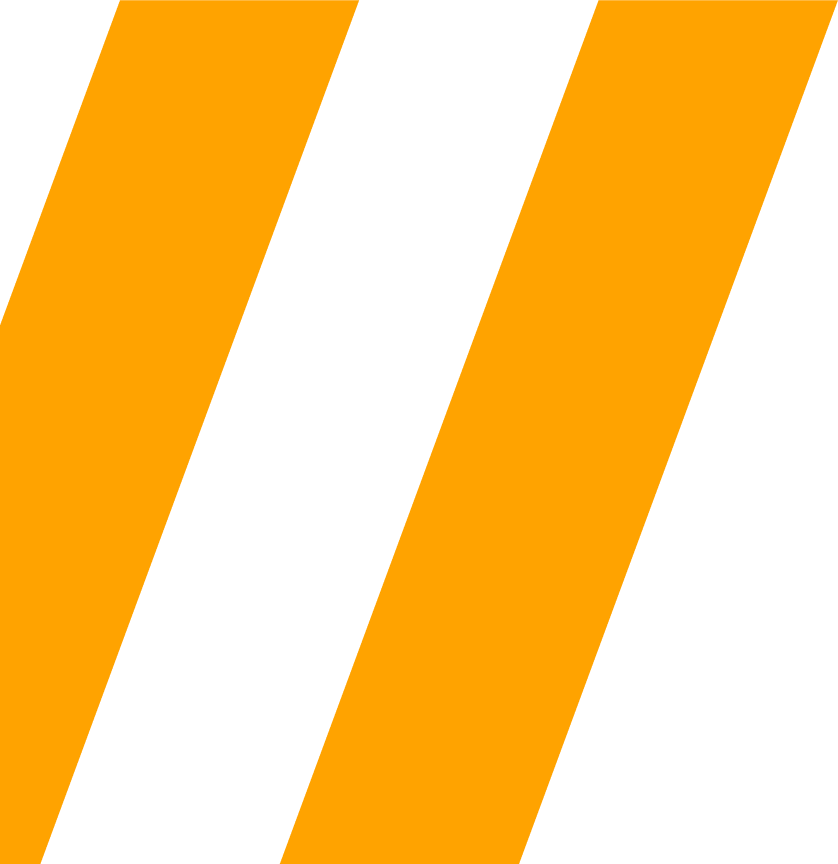
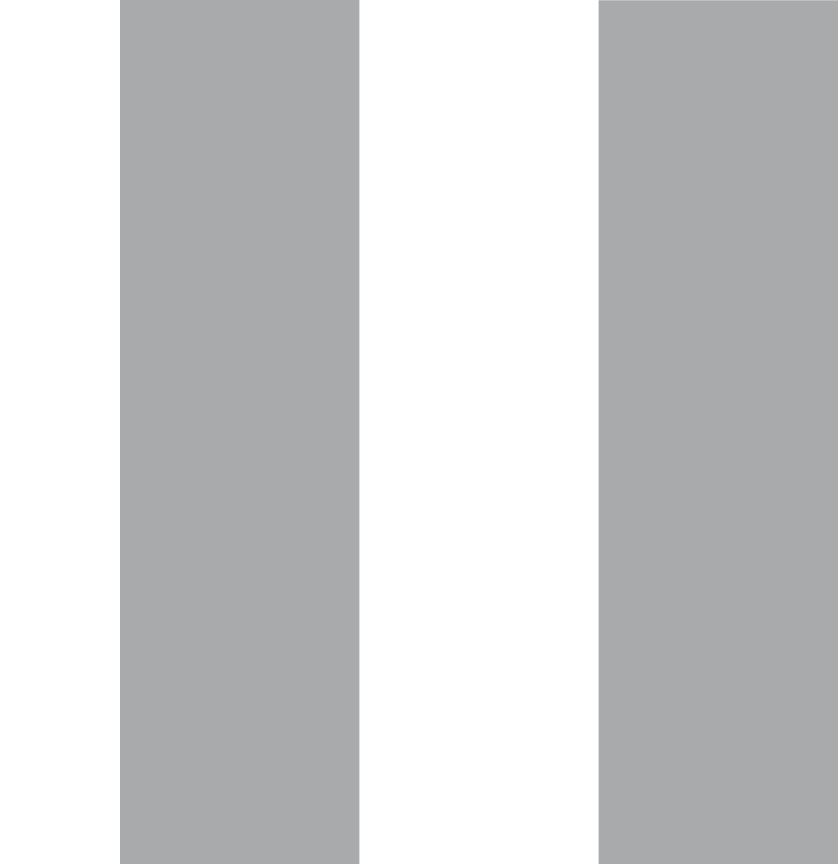
Key takeaways from the project
Quality Documentation
A new hold point in the quality documentation detects Super T Beam installation issues early, preventing latent structural issues in the overall project.
Collaborative Safety Processes
Collaborative safety processes and effective communication between engineers and the safety team resulted in excellent problem solving and project timeline results.
Overview
The long-awaited, environmentally considerate, and largest transport infrastructure project in Northern Victoria has been enthusiastically welcomed by local communities and road users communities who live, work and travel between Echuca and Moama.
Background
The Echuca-Moama Bridge Project, a highly anticipated and environmentally conscious infrastructure project, has been warmly welcomed by local communities and travelers between Echuca and Moama.
We were able to deliver the bridges on the Victorian Approach Spans, which included in-situ concrete construction works, installation of concrete Super Tee Beams, and the design and implementation of temporary works to facilitate these processes.
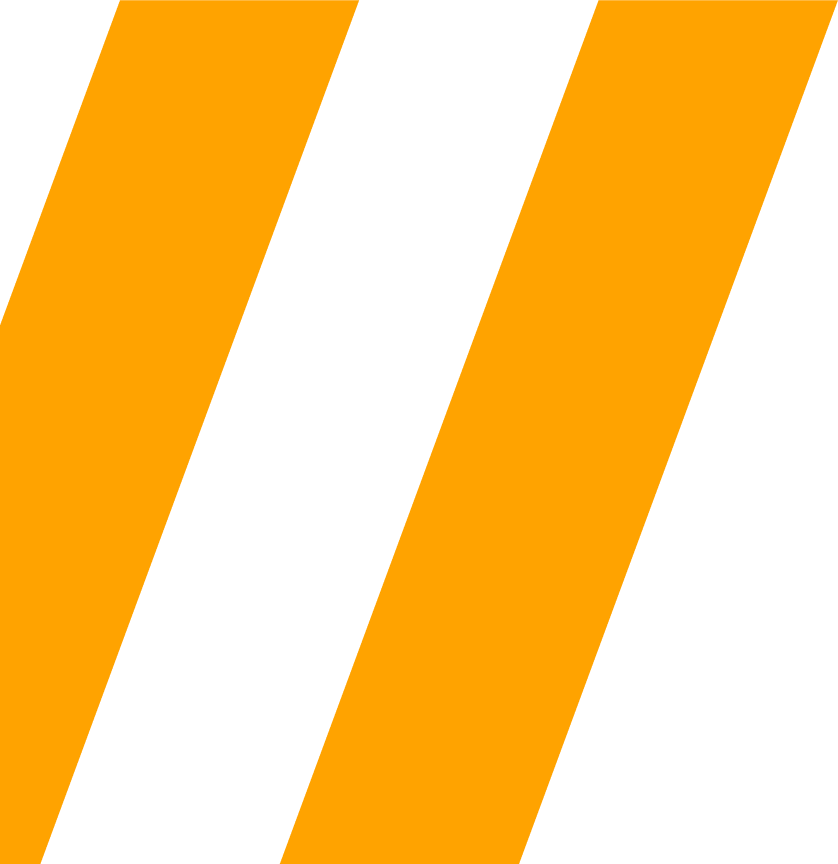
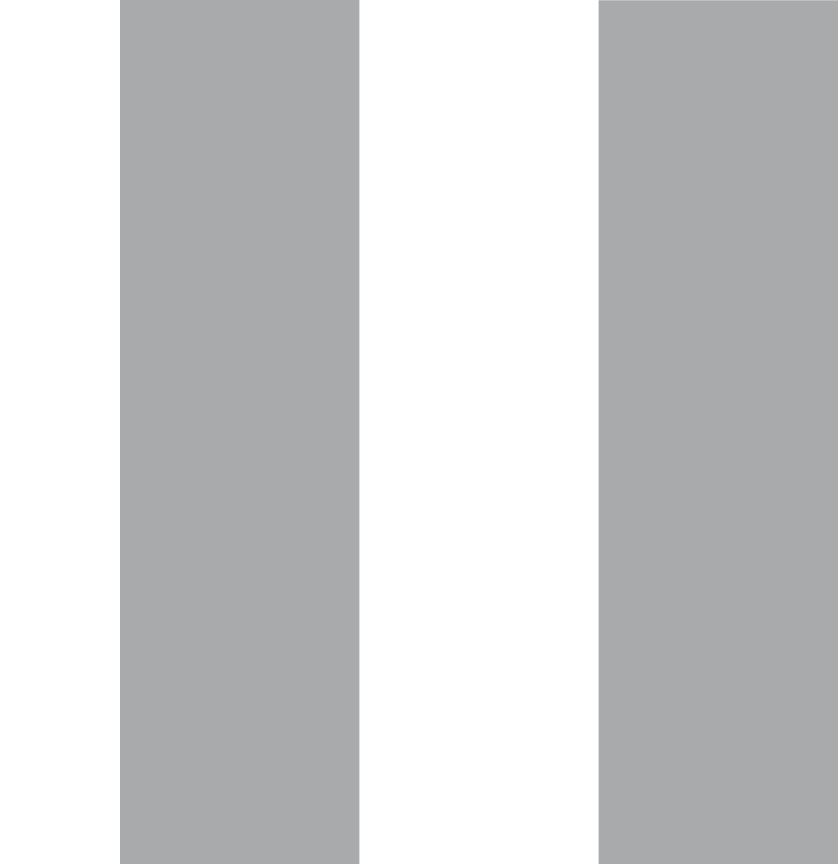
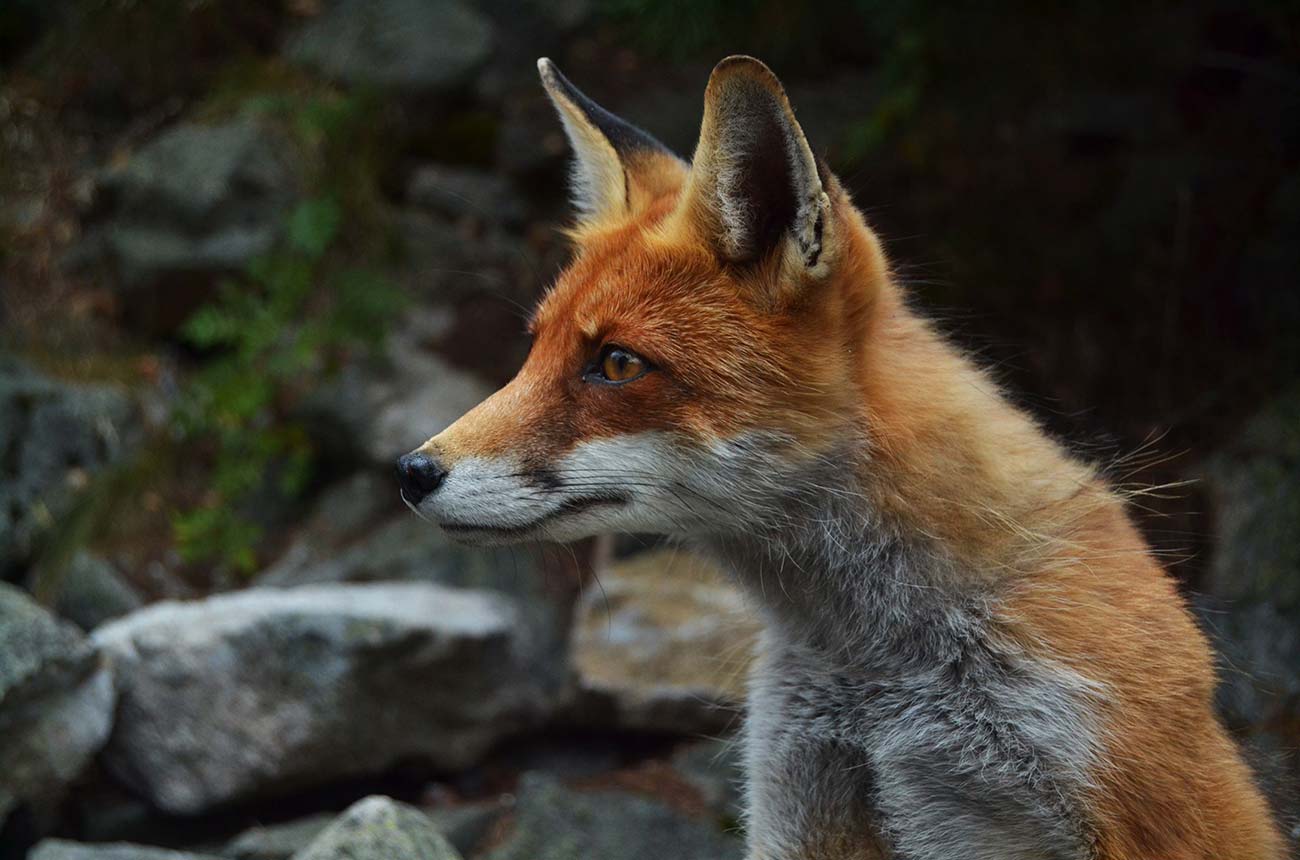
Method
During the installation of Super Tee Beams for the first span, we discovered that the elastomeric bearing pad was not resting completely flat and in full contact with the concrete pedestal. We immediately initiated discussions with the designers and construction team to investigate the issue, which revealed that the concrete pedestal was not completely flat. To mitigate this risk and ensure the success, safety, and timely delivery of the project, a methodology for rectification works was developed.
The crosshead was to be levelled for the extents of the jacking plate to provide a flat surface for the hydraulic jacks. Temporary props were installed to the Super Tee beams being jacked up, using existing ferrules in Super T diaphragms to account for any lateral movement. Two jacking plates were placed on the crosshead with two hydraulic jacks placed on top. Two hydraulic jacks with equal force were used to raise the beam to allow for the elastomeric bearing to be removed. A hardwood block was placed at the rear of the bearing pedestal to support the Super T in the event of the hydraulic jacks failing. Remedial works were completed on the pedestal to ensure a flat surface was achieved. The engineers and quality assurance team inspected and signed off on the remedial works before the bearing was installed and the jacks were lowered.
To ensure the quality of the rectification works, temporary works designers verified that the works could be conducted safely. The methodology was also verified by permanent designers to check the global stability and structural impacts of the beam during the rectification works. Additionally, a new hold point was added in the Inspection Test Plan prior to installation of the elastomeric bearing, which was signed off by engineers and the client quality representative.
The MBB difference
Our collaborative safety processes and effective communication between engineers and the safety team allowed us to detect the Super T Beam installation issues early and prevent latent structural issues in the overall project.
Results
The successful completion of the rectification works not only ensured the safety and quality of the project but also helped maintain the project timeline, resulting in a scenic bridge will ease traffic congestion during peak periods & ultimately improve overall safety for all road users.
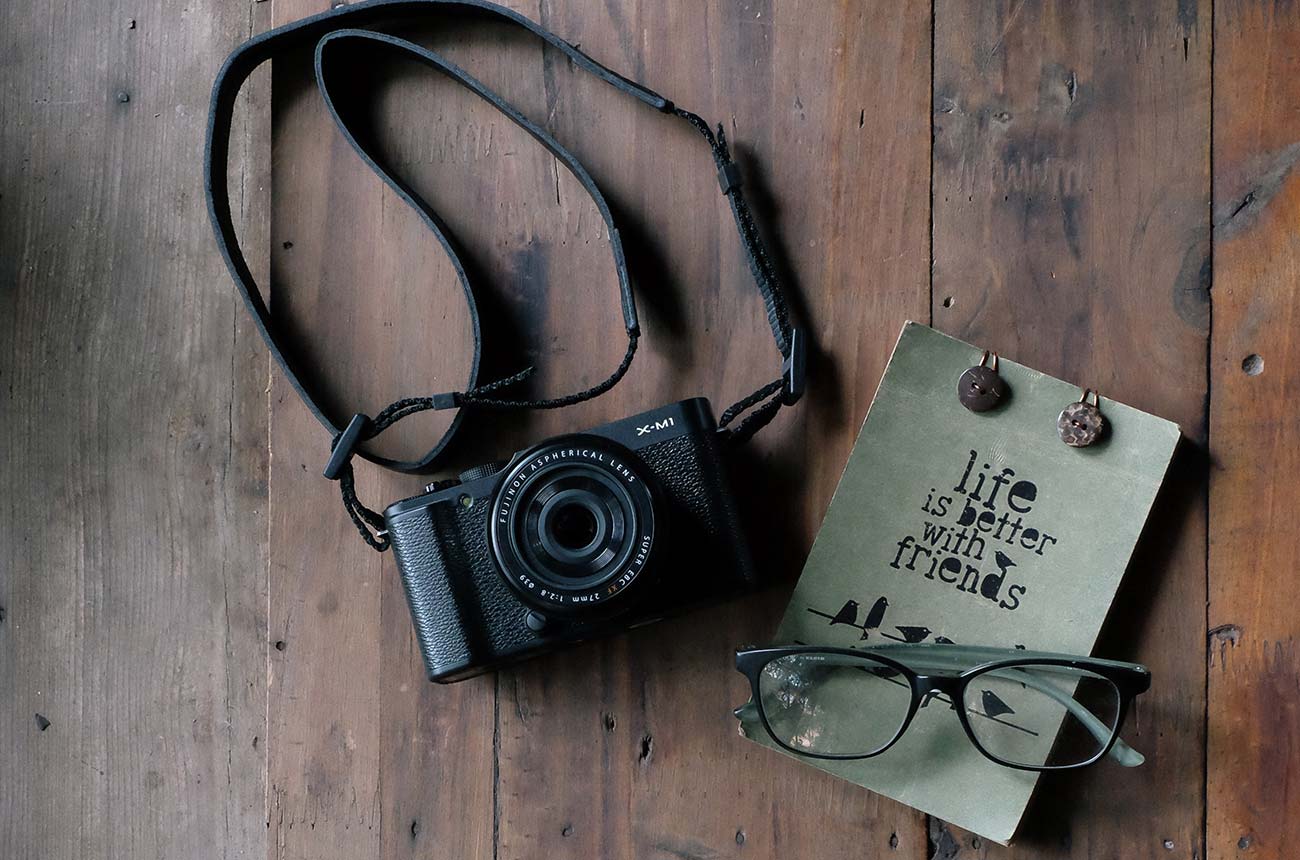